3.1 Conceptual Modelling
NOD
How conceptual models are used to communicate with yourself and others and how they vary in relation to the context.
The purpose of conceptual modelling is to outline the principles, processes and basic functions of a design. It originates from ideas in the designer's mind and is used to illustrate them to others, helping them to understand relationships, data, processes and more.
It is a representation of reality that can be made with various techniques for all kinds of situations and purposes.
CONCEPTUAL MODELLING TOOLS
How the designer visualizes concepts, design thinking and learning.
Flow charts
ADVANTAGES AND DISADVANTAGES OF CONCEPTUAL MODELLING
Advantages -
- Puts abstract ideas that originate from the mind into a visible and understandable form.
- Supports project planning.
- Explains features in data sets.
Disadvantages -
- Assumptions are made that in reality may not work.
3.2 Graphical Models
NOD
2D AND 3D GRAPHICAL MODELS
How graphical models are used to communicate with yourself and others and how the choice of graphical models vary in relation to the context.
Graphical models are used to portray how a concept will look in terms of size and aesthetical form. Freehand drawings are used in the early stages and developed to explore dimensions and form (3D - isometric drawings) and construction details and sizes (2D - orthographic drawings).

Advantages -
- Quick visual images to help develop ideas.
- Can communicate ideas to consumers/clients/others.
- Idea behind image can be explained.
- Encourages creativity.
Disadvantages -
- Can not be easily manipulated.
- Interpretation of the model is varied.
- Technical drawings may be difficult to understand.
PERSPECTIVE, PROJECTION AND SCALE DRAWINGS
Perspective - A 3D drawing that includes vanishing points.
- Allows us to consider spatial arrangements such as foreshortening.
- Visually accurate representation that can illustrate design to non-technical people.
- Allows us to display construction details and sizes which can be scaled up or down as needed.
SKETCHING VERSUS FORMAL DRAWING TECHNIQUES
Sketching
- Allows ideas to be visually communicated easily without technical aids.
- Used early in the design process to document ideas.
- Allows the designer to communicate ideas and consider the implications for further development.
Advantages -
- Details such as sizes and dimensions can be shown.
- Drawing can be used to manufacture the product.
- Allows more accuracy to be shown.
- Different views of the object can be seen.
Disadvantages -
- Drawing is time consuming.
- May require higher level of skill compared to free-hand.
- Drawing instruments and technical aid equipment is needed.
To allow further details and ideas to be explained, designers may draw an assembly or part drawing.
Advantages -
- Illustrates how the product is assembled.
- Displays how the product works.
Disadvantages -
- Drawing is time consuming.
- May require higher level of skill compared to free-hand.
- Expensive.
NOD
Applications of physical models and the use of instrumented models to measure product performance level and facilitate continuous formative evaluation and testing.
SCALE MODELS
Physical representation of an object with all aspects accurately maintained in the model.
- Material properties - Model's interaction with outside world is related to the original object's interaction.

AESTHETIC MODELS
Models that look realistic similar to the product it represents.
They are made to look and feel like the final product and is used for various purposes such as ergonomic testing and evaluation of aesthetic appeal.
- Allows designer to visualize the design.
- Non-working (for show) but shows how the object will look aesthetically.
- Expensive to produce.
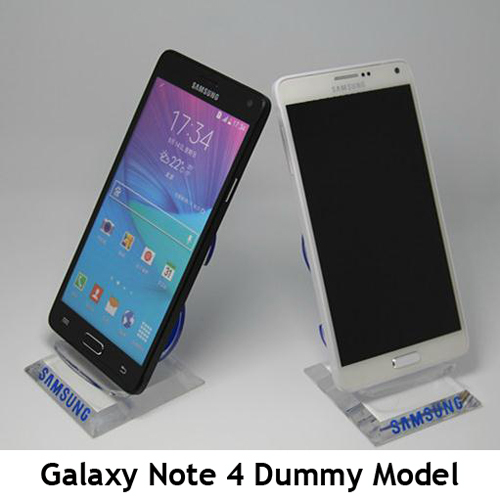
MOCK-UPS
Used for teaching, demonstration, design evaluation and promotion.
Can be a full-sized or scaled model of an object.
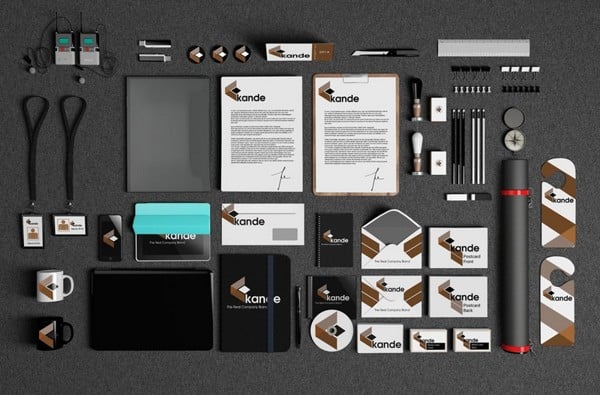
PROTOTYPES
Models intended to be used to test concepts and processes to allow the designer to enhance its function.
Allows designers to discover specifications for real and working systems rather than theoretical ones.
- Developed to work from two perspectives: the designer who learns by developing the product and the user who can provide the designer with feedback and user interaction.
- Can be produced at different fidelities: low (conceptual representation), medium (represents various aspects of ideas), high (mock-up, close to final product). This depends on the context in which it will be used.

INSTRUMENTED MODELS
Models that consider the dimensions, weight proportions and articulation of an object and used to made to test the dynamic behaviour of the product such as velocity, force, bending, folding or torque.
Examples include crash testing cars or testing aircraft testing in wind tunnels.
- Includes the ability to take measurements and provide accurate quantitative feedback which can be analysed later on.
- Can be used to investigate product's reaction to natural surroundings.
ADVANTAGES AND DISADVANTAGES OF PHYSICAL MODELLING
Advantages -
- Shape, proportion and aesthetics can be easily communicated to the user (car shows).
- Provides a realistic visual image.
- Allows design to be understood by non-technical audience.
- Allows design to be communicated to a wide range of people.
- Allows for user trials and testing ergonomics.
- Consideration of environment can be done and improved by testing.
- Production is time consuming.
- High level of skill required to produce models.
- Resources are needed to produce models such as machinery, raw materials and equipment.
- Bad on the environment as producing models requires energy and raw materials plus having to be disposed of later on.
- Expensive to product high-quality models.
- Models are not adjustable or flexible after produced.
- Scaling errors could be occur resulting in inaccurate testing.
3.4 Computer-aided Design (CAD)
NOD
TYPES OF CAD SOFTWARE
CAD software comes in many different:
- Types
- Prices
- Features
- Quality
SURFACE AND SOLID MODELS
Surface modelling - Modelling the exterior of the object as a thin skin created using lofts and curves.
Solid modelling - Modelling the object with its geometric mass by creating a solid base and then adding and taking away from the base to include features such as extrude, revolves, chamfers, etc.
DATA MODELLING INCLUDING STATISTICAL MODELLING
How data models structure data through database models.
VIRTUAL PROTOTYPING
VP is modelling a system to simulate and visualize how it operates under real-world conditions and is usually done using a software. Designers can build and test virtual prototypes (parts or entire structure) on a computer and analyze its behavior before actually manufacturing it.
This may reduce the time and cost of development as well as improving the quality of the designs.
BOTTOM-UP AND TOP-DOWN MODELLING
Top-down modelling - start with the design criteria and then create components that meet the specific criteria. Parts added are adjusted to fit with the first part.
Bottom up modelling - the parts are drawn individually and then assembled together in the order they would be assembled in manufacturing. The parts may sometimes not fit together and components will have to be redrawn.
DIGITAL HUMANS
How they can be used to simulate design scenarios and context.
Computer simulations of the human body's biological and mechanical aspects that allow us to develop products to suit human requirements more accurately and efficiently.
- Motion capture - recording movements using sensors and markers allowing us to develop a digital representation of the movement, cutting down on animation.
- Haptic technology - simulation of the sense of touch using forces equivalent to those in the real world allowing the user to feel and touch virtual objects and model the surface properties of an object.
- Virtual reality (VR) - computer generated 3D environment that the user can interact with through wearable technology.
- Animation - simulation of various scenarios and can monitor the safety of production by modelling the process using animation.
Comparison of FEA with testing physical models
Use of FEA systems when designing and developing products.
Modelling the material or design under stress, strain or heat using 3D computer software that can calculate the stress exerted on specific parts.
It helps to predict the life of the material of product where cracks or damages are likely to occur. It can help to identify failures due to unknown stress factors in the material and is more efficient and less costly than manufacturing and testing each sample.
ADVANTAGES AND DISADVANTAGES OF COMPUTER-AIDED MODELLING
Advantages -
- Complicated drawings can be saved and modified efficiently.
- Data is easily shared.
- Can be used with CAM and CNC machines.
- Software and equipment is expensive.
- Training is needed to acquire skills to operate and as technology develops, skills need to be updated.
- May not be realistic as a physical model.
3.5 Rapid Prototyping
NOD
Different types of 3D printing techniques.
STEREOLITHOGRAPHY
Using liquid plastic which is cured or hardened to form a solid object.
LAMINATED OBJECT MANUFACTURING (LOM)
Sheets of paper, plastic or metal laminates are glued together using a heat roller and then cut into shapes using a knife or a laser cutter.
FUSED DEPOSITION MODELLING (FDM)
Using thermoplastics that are heated to its melting point and layered to create a 3D object. (3D printers)
SELECTIVE LASER SINTERING (SLS)
Using a a laser to trace the object onto a thin layer of powder (plastic), heating it up so the particles fuse together to form a solid object. This is done in layers.
ADVANTAGES AND DISADVANTAGES OF RAPID PROTOTYPING TECHNIQUES
Advantages -
Disadvantages -
0 comments :
Post a Comment